The Thermal Challenge: How to Master Fan Selection for Extreme Industrial Conditions
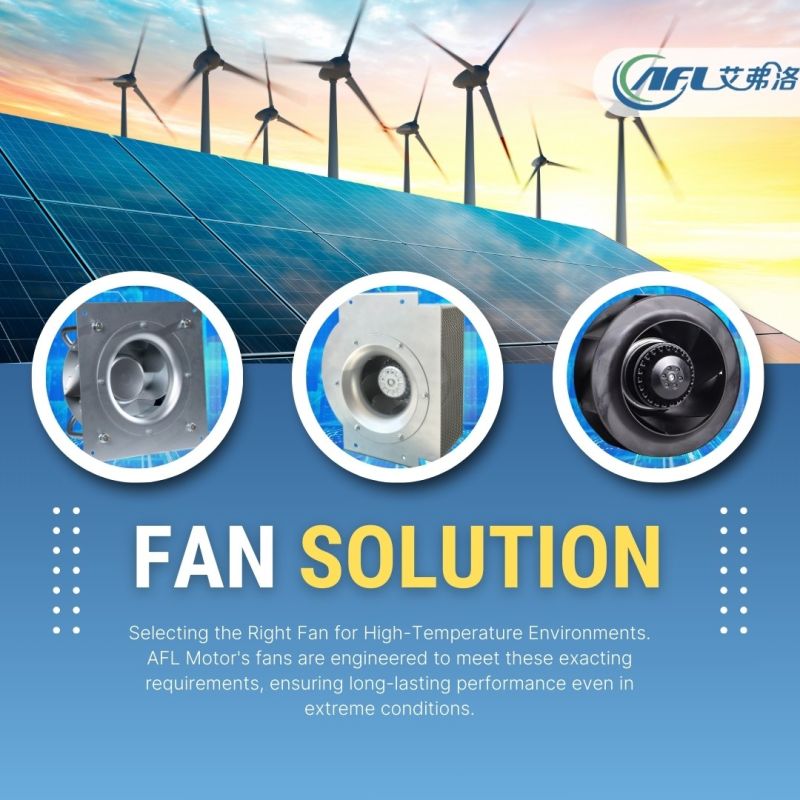
The Critical Role of Selecting the Right Fan for High-Temperature Environments: An Engineering Imperative
Managing heat is a pervasive and potentially destructive challenge within industrial systems. In specialized sectors such as wind energy storage, advanced power inverters, and numerous other high-temperature applications, the stakes are exceptionally high. The reliable operation of critical equipment fundamentally depends on effective thermal management, a process where the industrial fan often plays an underappreciated, yet central, role. Selecting the right fan for high-temperature environments isn't merely a procurement decision; it is a critical engineering imperative that directly impacts system performance, longevity, and ultimately, profitability.
Consider the unforgiving conditions these components routinely encounter. A power inverter, for instance, generates substantial heat during electrical power conversion, frequently operating within confined enclosures. Wind energy storage units, while not always intrinsically "hot," often reside within large systems exposed to ambient temperatures that can fluctuate dramatically, or they may house components that inherently generate significant heat. In such scenarios, a standard fan is simply insufficient. The challenge extends beyond merely circulating air; it demands consistent and reliable performance even when ambient temperatures soar, components are radiating heat, and continuous operation is non-negotiable. Common engineering pain points include premature component failure, system downtime, costly repairs, and a perpetual struggle against thermal runaway. This underscores precisely why a meticulous approach to selecting the right fan for high-temperature environments is so crucial.
Engineering for Endurance: Advanced Heat Dissipation in High-Temperature Fans
One of the foremost considerations in selecting the right fan for high-temperature environments is the fan's inherent ability to efficiently dissipate its own heat. This goes far beyond just moving a volume of air; it delves into the precise design of the fan's motor, bearings, and overall structural integrity.
Advanced heat dissipation structures are not optional in these applications; they are fundamental. This involves optimizing the motor's winding materials for superior temperature ratings, incorporating specialized bearing lubricants that maintain stability and do not degrade under thermal stress, and designing the motor casing itself to function as an effective heatsink. For instance, the use of finned aluminum motor bodies or strategically placed internal cooling channels can significantly enhance convective heat transfer from the motor components to the surrounding air. This engineering ensures that even when the high-temperature fan operates within an already elevated ambient temperature, its own internal components remain within their safe operating limits. Collaboration with material science experts is essential to guarantee that every constituent part, down to the smallest wire insulation, can consistently withstand the specified thermal envelope without degradation. This rigorous approach ensures that these high-temperature fans continue to operate efficiently even in demanding external environments, thereby protecting the fan itself while fulfilling its primary duty of cooling other critical equipment.
The Unseen Shield: Custom Housing and Temperature-Resistant Design for High-Temperature Fans
Another critical aspect when selecting the right fan for high-temperature environments is the integrity of its physical structure. The fan's housing and internal components must not only endure high heat but also maintain their structural stability and performance characteristics over extended periods.
AFL Motor's commitment to this principle is evident in their specially designed fan casings. This goes beyond mere aesthetics; it involves engineering materials and geometries that provide enhanced durability against elevated temperatures. Standard plastics or thin metals can easily warp, crack, or degrade rapidly when subjected to continuous thermal stress. Specialized polymers and robust metal alloys are utilized to maintain structural integrity and precise tolerances even under prolonged exposure to high temperatures. For example, in applications where the high-temperature fan may be in close proximity to a primary heat source or within an enclosure reaching 80°C (176°F) or more, the fan casing itself becomes an integral part of the thermal management solution, not simply a protective shell.
Furthermore, a truly temperature-resistant design extends to every internal component. This includes specialized electronics within the fan's motor control unit that are specifically rated for higher operating temperatures, wiring with high-temperature insulation, and even fasteners engineered to resist thermal expansion and contraction cycles. A single weak link in the thermal chain can compromise the reliability of the entire system. This holistic design approach ensures that these high-temperature fans maintain optimal performance, significantly reducing the risk of premature failure and, consequently, minimizing costly downtime for critical equipment in industries where continuous operation is paramount. This robust engineering minimizes thermal stress on the fan itself, allowing it to reliably function as a cooling agent for other sensitive components, even in the most challenging thermal conditions.
Built for Extremes: Beyond Just Heat Resistance in Industrial High-Temperature Fans
While high-temperature resistance is a primary concern, selecting the right fan for high-temperature environments frequently necessitates considering a broader spectrum of extreme demands. Industries such as wind energy and power conversion do not merely operate at elevated temperatures; they can also be subjected to significant vibration, strict air pressure requirements, or the need for exceptionally large airflow capacities.
These high-temperature fans are engineered to handle such multifaceted challenges. For instance, in power inverters, fans often need to generate high air pressure to efficiently push air through dense heat sinks or highly confined internal pathways. This requires impellers and motors specifically designed for strong static pressure development, rather than just high airflow volume. For applications demanding large-scale cooling, a high airflow capacity is critical, necessitating larger, yet still thermally resilient, fan designs.
Moreover, vibration resistance is a non-negotiable factor. Equipment in wind energy storage or power generation frequently produces vibrations that can rapidly degrade standard fan bearings and mountings. These designs incorporate robust bearing systems and specialized mounting solutions that effectively absorb and mitigate these stresses, ensuring long-term mechanical integrity. This multi-faceted design philosophy, honed through years of practical application and technical cooperation with leading research institutes, ensures that these high-temperature fans are truly robust solutions capable of operating seamlessly under continuous thermal stress, vibration, high air pressure, and demanding airflow capacities – providing an optimal balance of reliability, performance, and energy efficiency. In these critical industries, a fan is recognized not just as an accessory, but as a core component directly impacting the system's operational uptime and lifespan.
The Strategic Choice: Selecting the Right Fan for High-Temperature Environments
The implications of making an incorrect fan choice in high-temperature environments can be severe, leading to reduced equipment lifespan, frequent maintenance requirements, and potentially catastrophic system failures. This is precisely why a proactive and informed approach to selecting the right fan for high-temperature environments is crucial for engineers and procurement managers alike.
When making this vital decision, several key factors warrant careful consideration:
-
Temperature Rating: Verify that the high-temperature fan's continuous operating temperature range matches or exceeds the maximum ambient and internal system temperatures it will encounter.
-
Material Science: Ensure that the casing, impeller, and motor components are constructed from materials demonstrably proven to withstand thermal stress without degradation over time.
-
Heat Dissipation Design: Confirm that the high-temperature fan itself incorporates design features specifically aimed at effectively managing its own internal heat generation.
-
Vibration and Pressure Resilience: Beyond thermal resistance, assess the fan's capacity to withstand other physical stresses inherent to the application, such as vibration or the need for high static pressure.
-
Reliability Track Record: Prioritize manufacturers with a proven history of designing and producing high-temperature fans for extreme conditions, supported by relevant certifications, rigorous testing protocols, and established industry partnerships.
AFL Motor is dedicated to providing solutions that embody these principles. Their focus on efficient heat dissipation structures, custom high-temperature resistant housings, overall temperature-resistant designs, and robust build quality for extreme demands like vibration and high air pressure positions them as a leader in this specialized field. In industries where uptime and reliability are paramount, their high-temperature fans are engineered not just to "handle the heat," but to conquer it.
Selecting the Right Fan for High-Temperature Environments FAQ
Q: What safety certifications should be sought when selecting a fan for high-temperature environments?
A: When selecting the right fan for high-temperature environments, crucial safety certifications often include CE (Conformité Européenne) for European markets, which indicates compliance with health, safety, and environmental protection standards. Depending on the specific industry and geographical region, other relevant certifications might include UL (Underwriters Laboratories) or IEC (International Electrotechnical Commission) standards, which address electrical safety, thermal performance, and specific hazardous location ratings. It is always advised to verify the certifications relevant to your specific application and target operating region for any high-temperature fan.
Q: What is the typical warranty policy for fans explicitly designed for high-temperature environments?
A: For high-temperature fans specifically engineered for such environments, manufacturers often provide a warranty reflecting their robust design and high-quality materials. While terms vary by product and manufacturer, a typical warranty period might range from 1 to 3 years or longer, covering manufacturing defects and material failures under specified operating conditions. It is always best to consult the manufacturer's specific warranty documentation for detailed coverage information on their high-temperature fans.
Q: How is the quality control process managed for fans developed for extreme conditions like high temperatures?
A: The quality control process for high-temperature fans designed for such environments is exceptionally rigorous. It commences with meticulous material verification (e.g., ensuring high-temperature polymers and specialized alloys meet specifications) and extends through every manufacturing stage. In-process checks are conducted for dimensional accuracy and assembly integrity, followed by comprehensive final performance testing. This includes thermal cycling tests in specialized chambers, vibration testing, and assessments of airflow, pressure, and acoustic performance to simulate extreme operating conditions and guarantee the high-temperature fan's sustained reliability and performance at elevated temperatures.
Q: What specific "advanced heat dissipation structures" are integrated into these high-temperature fans?
A: When referring to "advanced heat dissipation structures" in high-temperature fans, this pertains to engineering features that enhance the fan's ability to shed its own internal heat. This can include: finned motor housings made from highly conductive materials (such as aluminum) to increase surface area for convective cooling; optimized internal airflow paths within the motor designed to guide heat away from critical components; and the utilization of high-temperature rated bearings and lubricants that dissipate heat more effectively and maintain stability under elevated thermal conditions. These design choices ensure the high-temperature fan itself remains within its thermal limits while simultaneously cooling other equipment.
Q: How does custom housing enhance durability against high temperatures compared to standard fan casings?
A: Custom housing in high-temperature fans significantly enhances durability compared to standard casings by utilizing materials specifically selected for their superior thermal properties. This involves employing high-performance engineering polymers or specialized metal alloys that resist warping, embrittlement, or degradation when exposed to continuous high temperatures. Unlike standard plastics that may deform or become brittle, these custom materials maintain their structural integrity, precise dimensions, and protective capabilities, thereby ensuring reliable operation and extended longevity even under prolonged thermal stress in demanding industrial environments for any high-temperature fan.
Q: What specific "temperature-resistant design" elements extend beyond just the casing and motor in a high-temperature fan?
A: A truly "temperature-resistant design" for high-temperature fans encompasses elements beyond just the casing and motor. It includes: high-temperature rated wiring and insulation that will not melt or degrade; electronic components within the fan's control board that are specifically chosen for their elevated temperature tolerance; specialized potting compounds or sealants that maintain integrity at high heat; and fasteners or mounting hardware that resist fatigue from thermal expansion and contraction cycles. Every component is carefully selected and tested to ensure the entire high-temperature fan system functions optimally and reliably in continuous high-temperature conditions.
Q: How do these high-temperature fans manage "vibration resistance" in industries like wind energy storage?
A: For industries such as wind energy storage, where equipment can experience significant vibrations, these high-temperature fans are designed with enhanced vibration resistance. This is achieved through: robust bearing systems (e.g., high-quality ball bearings) that are less susceptible to wear from constant vibration; precision balancing of impellers to minimize inherent vibrations; and durable mounting solutions (e.g., rubber isolators or specialized anti-vibration mounts) that effectively absorb and dampen external shocks and vibrations. This multi-faceted approach ensures the high-temperature fan maintains mechanical integrity and quiet operation despite dynamic external forces.
Q: What is the distinction between "high air pressure" and "large airflow capacity" when selecting a high-temperature fan?
A: These are distinct, though often related, high-temperature fan performance characteristics. "High air pressure" (or static pressure) refers to the fan's ability to overcome resistance within a ducted system, effectively pushing air through components like filters, grilles, or long runs of ductwork. It quantifies the force the fan can generate. "Large airflow capacity" (or volumetric flow rate, typically measured in CFM or m³/h) refers to the sheer volume of air the fan can move per unit of time. A high-temperature fan can possess a large airflow capacity but struggle with high pressure, or conversely. Selecting the right fan for high-temperature environments often necessitates a balance of both, depending on whether the primary requirement is to overcome system resistance or simply to move a substantial volume of air for cooling purposes.
Q: Why is it critical for high-temperature fans used in power inverters to be built for "extreme demands"?
A: It is critical for high-temperature fans in power inverters to be built for "extreme demands" because inverters frequently operate under conditions that combine high internal heat generation with potentially high ambient temperatures. Beyond just temperature, they typically require high static pressure to effectively push air through compact, dense heat sinks and constrained internal pathways. Furthermore, power inverters can experience significant electrical and mechanical stress, necessitating high-temperature fans that are not only thermally robust but also highly resistant to vibration and exceptionally reliable for continuous, often mission-critical, operation. The failure of such a high-temperature fan can lead to immediate and costly inverter shutdown or damage.
Q: How does AFL Motor ensure its high-temperature fans achieve "the perfect balance of reliability, performance, and energy efficiency" for high-temperature applications?
A: AFL Motor achieves this balance through a comprehensive engineering approach. Their technical cooperation relations with leading scientific research institutes and insights from their five renowned technical consultants (including a senior German expert) drive their ongoing R&D. They focus on intelligent, energy-saving designs, supported by 23 patents, ensuring their products—including their high-temperature fans—meet rigorous efficiency standards (e.g., ERP2015). This extensive R&D is combined with a steadfast commitment to durable materials and rigorous quality control, resulting in high-temperature fans that are not only high-performing and energy-efficient but also exceptionally reliable even in the most demanding high-temperature environments.
-
Beyond Basic Extraction: The Advanced Performance of EC Single Inlet Forward Centrifugal Fans
2025-06-27
-
A2D315S-7BM-AR02 AC Axial Fan for Energy Storage Cooling & Photovoltaic Systems
2025-06-19
-
Energy-Saving DC External Rotor Fans for Industrial Ventilation & Electronics Cooling
2025-06-19
-
AFL 400mm EC Backward Centrifugal Fans for HVAC & Industrial Ventilation Applications
2025-06-19